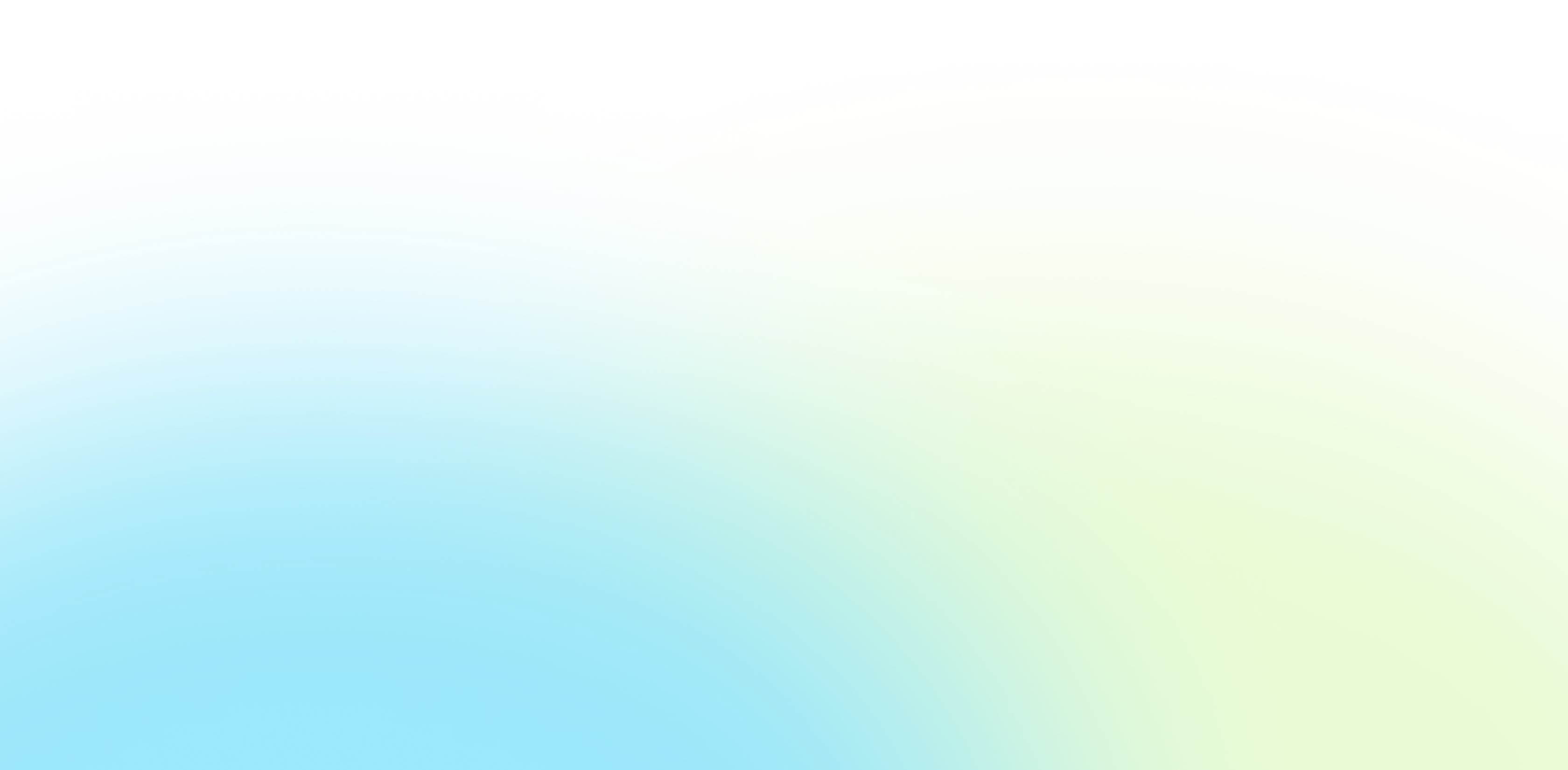
Innovative Solutions
from a Trusted Partner
Hagerman & Company is a full service solution provider. We offer a variety of customizable solutions to maximize the return on your technology investment.
Hagerman Professional Services
Sorry!
No items currently match your filtering criteria.
Reach out today to schedule your business consultation.
The following modules will only show up on dynamic pages, NOT this listing page.
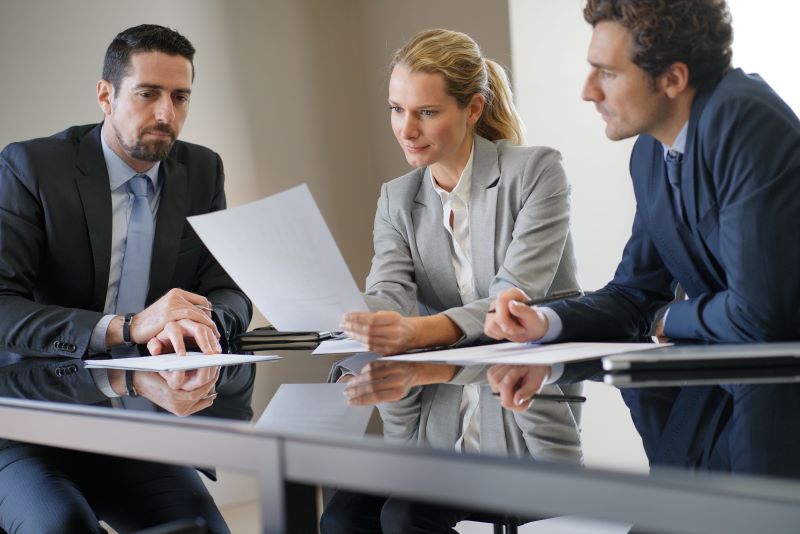
Why Choose Hagerman
Hagerman & Company has built our success not only on the quality of solutions that we offer, but also on the relationships we’ve built with our clients. To do this, we have adopted a comprehensive Customer Success strategy designed to drive increased long-term customer value, improve the customer experience, and ensure customer satisfaction. This philosophy is shared across our entire organization, including sales, marketing, service delivery, and back-office support.
As a solution provider, we offer the tools to make your company more efficient, productive, and most of all, profitable. We do this by offering best-in-class software paired with professional services delivered by an exceptional team of industry consultants, solutions engineers, and support staff.
Let's Talk Strategy
Hagerman & Company can customize a solution to meet your company’s strategic goals. We connect, improve and automate efficient systems within your organization so you can deliver more innovative solutions to your customers.
Contact us today to schedule a business consultation.